Two typographical errors occurred in the second article of ihis series. On p. 94, helow the illustration of enamelling tools, read "scorpers" instead of "scoopcrs"; on p. 92, in the receipt given for white enamel, read " 10 parts of calx to 16 parts of flux."
Champlevé enamel upon the precious metals, silver and gold, is done in identically the same manner as upon copper (see Part II. of this series). It is better to use silver a little above the standard, as it is more flexible; and gold ought not to be less than 18 carats. Enamel, practically speaking, after it has been fixed is neither expanded by heat nor contracted by cold. In this, of course, it is at variance with the copper, the silver, or the gold, and it is the constant effort of the one to throw the other off. And this accounts for several of the most important parts of the processes used in enamelling. In the case of the chanipleve process, it is the reason for the enclosing lines of metal and the keyed grounds; in cloisonne, the reason of the wire cloisons and of other essential parts of the processes, which I shall describe in their place.
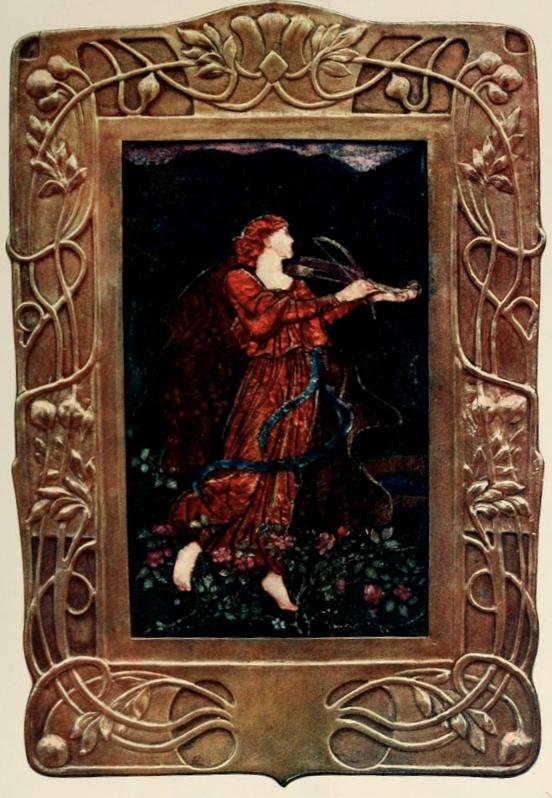
Good Tidings by the author.
After the work in the champleve process is finished one of the most important things is the gilding of the metal parts. This is generally done by a gilder. There are two methods of gilding. One is called " mercury-gilding " or "watergilding," and the other, "electro gilding." The first is done by an amalgam of gold and mercury, which, mixed with water, is painted on the metal, and then subjected to a heat sufficiently great to drive off the mercury, leaving the gold attached to the metal.
The process of electro-gilding is carried out by the use of an electric battery, in which the metal lines and parts not covered with enamel receive a fine deposit of gold. The gold may be afterwards brightened or burnished. It is often the unhappy experience of all enamellers who have entrusted their work to gilders to receive it back from them either wholly or partially destroyed. The principal causes — apart from those due to carelessness — are several. One is that, in the case of mercurygilding, the heat used to draw off the mercury has been too suddenly applied; or it may be that the acid employed in cleansing the metal has been allowed to undercut the enamel, so that any very slight friction would peel the enamel off at the parts thus undercut. The same cause in the process of electro-gilding would allow the gold to be deposited underneath the enamel, thereby lifting off the enamel in flakes. Therefore, it would be wise for an enameller to do his own gilding. An excellent description of the gilding processes may be found in Spon's Encyclopedia.
The design for champlevé enamelling should be done in a simple manner, and with as few lines as possible consistent with the technical necessity of holding the enamel, and the lines should be of such a thickness as to be readily seen. It is noticeable that colours of medium strength give greater breadth than those which are much lighter or darker than the metal, and that a certain degree of hardness is overcome by graduating the colour spaces, and also by engraving a pattern on the metal surfaces left bare of enamel. It is by such means that a certain hardness and tightness, observed in almost all modern objects of this kind, is avoided in the beautiful old work.
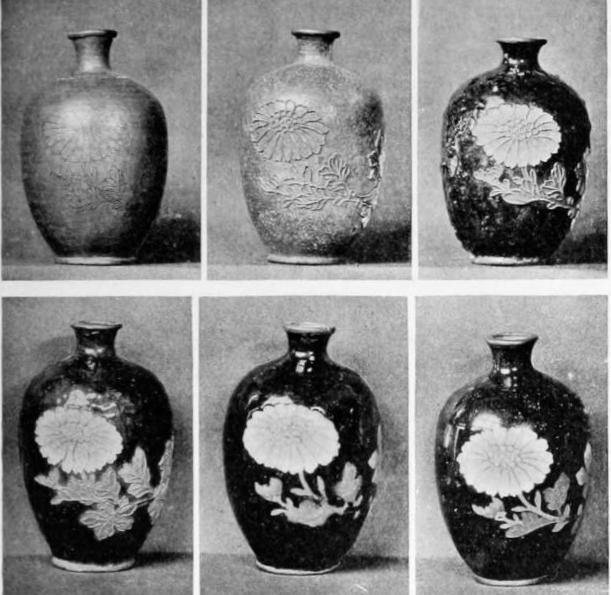
Vases showing the different stages of cloissonné enamelling. 1. The pattern outlined in India ink on the copper vase. 2. The wire soldered on to the vase. 3. First coat of enamel, fired. 4. Second coat of enamel, fired. 5. Third coat of enamel, fired. 6. Last coat of enamel, polished.
Bassetaille. — The word Bassetaille is derived from the two old French words, "basse" meaning low, and "taille," cut, — that is, "low cut," like an Egyptian bas-relief. It consists of a subject carved in low-relief below the general surface of the metal object; so that when the enamel is placed over the design the whole surface of enamel and metal is one, and the relief is seen through the transparent enamel. The tools employed for champleve may be used also for bassetaille. That they should be more numerous and with greater variety of shape of edge will depend upon the kind of work and the artist's choice. The whole process is exactly similar in other respects to that described under the head of champlevé, except that it is carving in relief and not merely sinking a flat space for the enamel inlay. The great example is the "Kings' Cup" at the British Musuem. There is another at King's Lynn, commonly known as the "Lynn Cup," which was done by this bassetaille method. It is to be observed that there is no metal division between the different coloured enamels in bassetaille. This is a great advantage: there is no necessity for a metal divisii n unless the enamels are very soft, in which case they are bad for any kind of work.
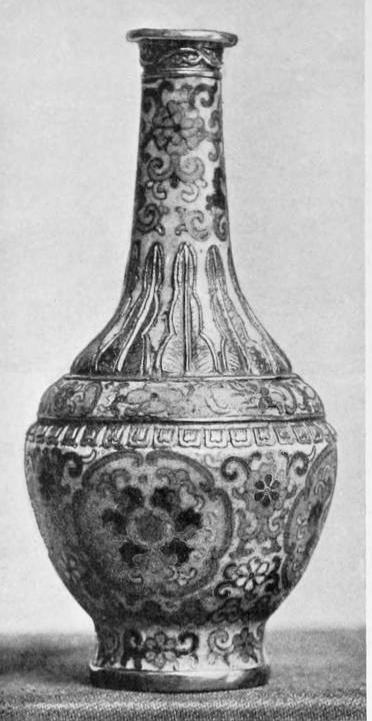
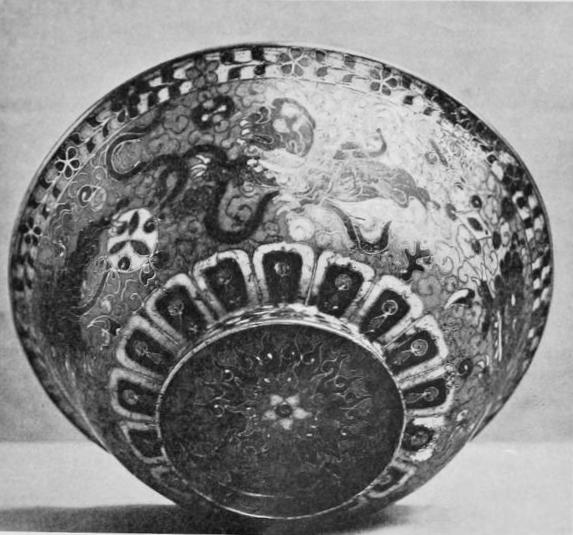
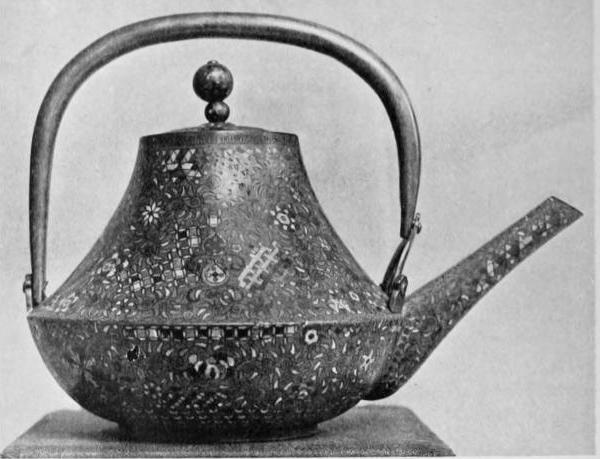
Left: Japanese cloisonné enamel vase. Imperial Institute).. Middle: Ancient Chinese cloisonné bowl. Imperial Institute). Right: Ancient Chinese cloisonné pot. Imperial Institute).
The method of enamelling after the subject has been carved is much the same in bassetaille as in champleve, the only difference being that, owing to the absence of a metal division, much greater care is required in keeping the edges of the colour quite clear and sharp and clean. The best way to do this is by adding a little gum tragacanth and water to each enamel, and by letting this mixture partly dry after it has been laid upon the metal; by this means a sharp clear edge is formed before the next colour is put in juxtaposition to it. Great care, again, must be taken in handling the work and in placing it into the furnace, for if any particles of enamel get moved out of their place, the edges of colour will be blurred after the firing. There are, indeed, many pitfalls in this bassetaille process, and you will find it a most valuable thing to test a small part of each enamel you intend to use. Yo\ this purpose I keep always by me some small pieces of metal ready prepared. When the metal is being carved, it is a great help to test the relief for enamel by mixing a little water-colour of the same tone as the enamel and floating it over the metal spaces polish. Each of these processes will be found of the greatest possible aid.
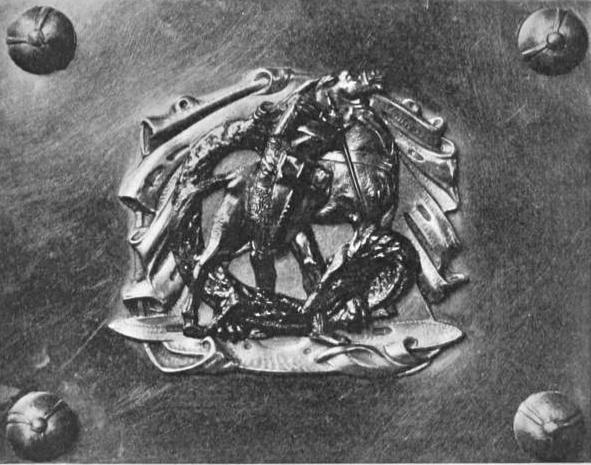
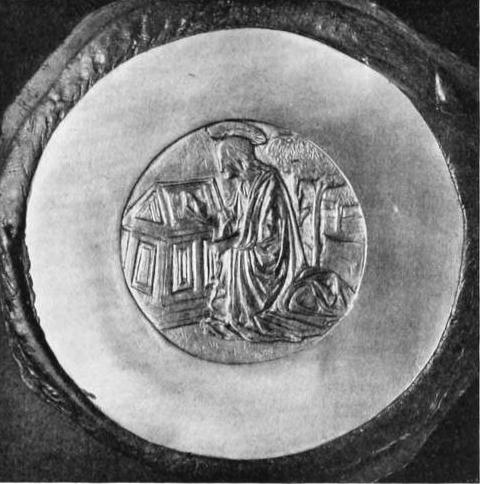
Left: Book cover in repoussé gold enriched with transparent enamel by the author. Right: Piece of silver fixed on pitch block, showing a figure in process of being carved for bassetaille enamel.
I have detailed the manner in which the engraving and carving for champleve and bassetaille are done. But I must note here that if it be desired to make a small cup, a tazza, plate or box, it will be necessary to have one or two other tools besides those pertaining to the art of enamelling. A few hammers are required, and a sand-bag, some stakes and mandrils, a vice, a blowpipe, a planishing hammer, and a bath for pickling. Supposing the article to be a bowl of four inches diameter and three in height, the mode of procedure is this. If we measure the height plus the diameter carved for the reception of the enamel.
Although the enamelling is difficult, the most difficult as well as the most important part is the carving of the metal. It requires the most accurate drawing and the most perfect mastery of the graver and scorper. Vou will see that there is a large amount of metal work of different kinds to do in order to become an enameller, and it is certainly of great assistance to serve an apprenticeship in engraving, in repousse work, in hard silver and gold soldering, and also, of course, in hammering and fitting. It is also advantageous to know how to a very strong hand to do this, do once round on each line, and then start on a fresh one, until you get to the outer edge; then take the metal to the blow-pipe and anneal it, softening the metal by making it red-hot and then letting it cool. All metals become hard and springy by hammering, and are softened by heat. After it is cold you repeat this process of hammering, until a deep saucer shape is obtained, then turn it over and put its edge on a curved stake of iron or steel, shaped conversely, corresponding to the design, and with well-regulated blows upon the parts immediately above the stake, go round it, turning it and beating it at the same time.
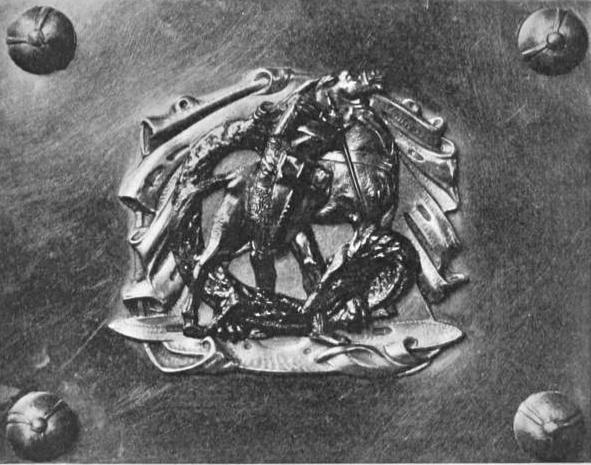
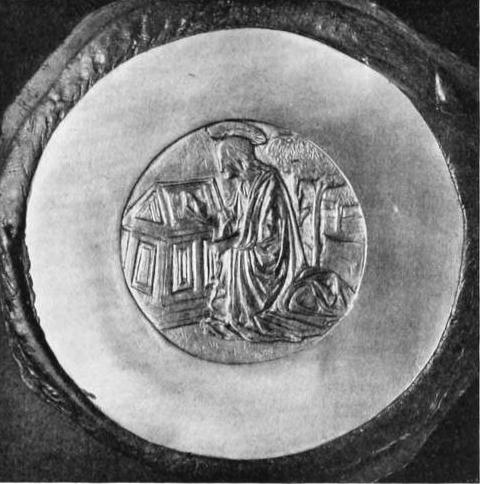
Left: Book cover in repoussé gold enriched with transparent enamel by the author. Right: Piece of silver fixed on pitch block, showing a figure in process of being carved for bassetaille enamel.
After each course of hammering it is necessary to anneal it, otherwise it will crack and split up; then continue to hammer in this way until the shape is complete. To put a cloisonne pattern upon this, you proceed in the following manner. The design is drawn or transferred upon the metal, and then with a steel point is scratched distinctly upon it, so that the design may be clearly seen during subsequent processes. The flat wire must now be thought of for the cloisons. In cloisonne enamelling on copper it should be of the hardest brass; silver wire should be used on silver; the width of the wire is partly determined by the character of the design and the aim of the artist, but one-twentieth of an inch thick commonly suffices for the boldest work. With round and flat-nosed pliers the wire is bent to the design, and with half the sum of these as the radius, we strike a circle on a piece of silver or copper of 14 metal gauge, then we describe a number of concentric circles, leaving a quarter of an inch between each circumference. Then the edge of the metal, slightly tilted on the sandbag, is held firmly in the left hand, and with a well-directed blow you strike it with the end of the hammer on the first line from the centre, then, while moving it slowly round at the same angle, the blows are struck regularly on this line. It requires then cut with cutting pliers at convenient points; and the pieces thus made are carefully gummed to cardboard, so that they may not he injured or lost. When all the cutting is done and the pieces have been bent accurately to the design, each cloison is soldered with silver solder to the metal bowl. The way to do this is somewhat complicated. The bowl has first to be cleaned wiih sulphuric acid and water, and afterwards thoroughly washed in water. A lump of calcined borax, moistened with water, has now to be rubbed upon a flat piece of rough slate until a thick paste is made; into this paste dip that edge of the wire which is to touch the bowl, and then lay it accurately in its place upon the surface of the metal. Next cut up into minute pieces some hard silver solder, and lay them on each side of the wire about one-eighih of an inch apart. Now lay the bowl — it must be firmly placed — on some coke or charcoal, and with a blow-pipe drive the flame gently all around the bowl, getting gradually nearer the wire. When the wire is touched by the flame, blow until it becomes red hot, so that the solder may flow along the cloison to hold it firmly in its place. You will first see the borax melt, and afterwards the solder. Take care not to melt the wire. By strictly observing these instructions the process will not be difiicult. Now take the bowl and put it into the sulphuric acid and water — about 20 parts of water to i of acid (this is called "pickle") — and leave it there until quite clean. The whole of this process must be repeated for every cloison. As regards the enamelling, it is done in exactly the same way as the enamelling of champleve work.
For encrustation enamelling it is sometimes desirable to prepare the design in repousse. To do this well, as indeed to do any other part well, a very great amount of practice is necessary.
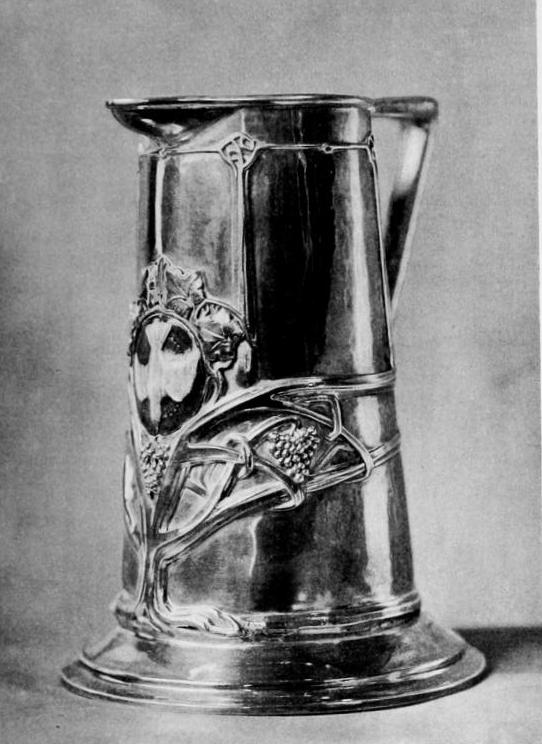
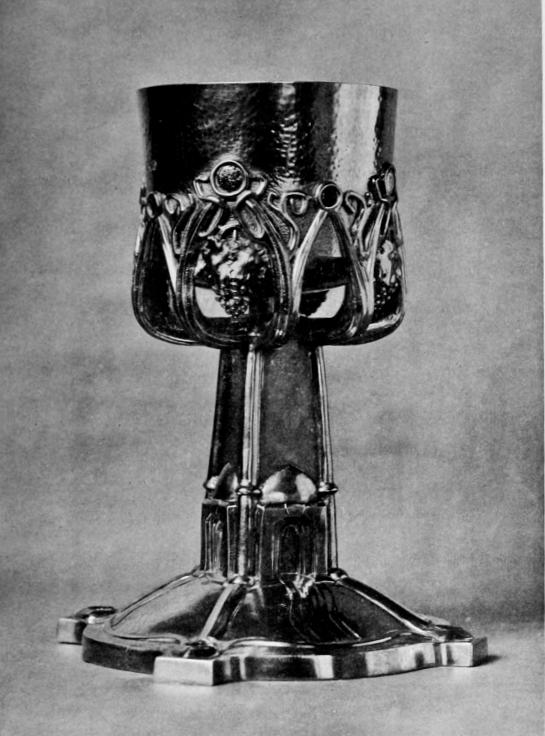
Chalices and flagon hammered and repousée silver with enamels by the author.
The implements required consist of one or two chasers, some hammers, and a considerable number of tools, which arc made of pieces of square steel about 5 ins. long, and ranging from 1/8 in. to 1/4 in. thick. The ends are shaped from a flat square to a round ball, from a thick tracer, which is like a chisel in shape with a blunt edge, to one which gives a hair-like line. It is best to make one's own tools. The rule is to make a tool that will shape the relief according to the design. For instance, a tool with a curved edge is used for a curved line, a round ball-ended tool to raise its own shape, a straight tool for a straight line, and so on. Pitch blocks are recjuisitc. I have already described how the pitch is mixed and spread when warm over the block of wood or stone or metal; and the reader will guess at once that the metal object must be pressed into the soft pitch until it sticks there. Then transfer your drawing in outline upon the wrong side of the metal, and then take a tracing tool — that is an edged tool, either curved or straight — and holding it at right angles to the metal, go gently yet firmly along the outline, sti iking the top of the tool with the hammer in a regular series of taps, moving the tool at the same time. For the raised parts softly rounded tools should be employed.
To remove the embossed plate from the pitch the metal must be warmed before the fire or by a blowpipe. To clean it use paraffin. Now place the embossed plate with its face upwards and work with the tools on its face, sharpening parts or softening others, until it is finished, then clean it as described. The manner of enamelling such work is of the simplest; it consists of overlaying the parts with a thin enamel both back and front, and firing. This is the way in which many of the most costly gold and silver ornaments, jewels and snuffboxes were made. — Alexander Fisher.
Bibliography
Fisher, Alexander. “"The True Art of Enamelling on Metals” The Studio Part II: 25 (1902): 108-18 University of Toronto copy made available online by the Internet Archive. Web. 25 January 2012.
Last modified 25 January 2012