Annunciation by the author — an example of champlevé enamel on silver.
There are two ways of interpreting the words "an enamel." They may signify the substance enamel, or may be applied to the completed work. The substance enamel is a vitreous compound that adheres to the surface of the metal upon which it is fused. Enamels are divided into three kinds, the transparent, the translucent, and the opaque. The transparent are those through which it is possible to see quite clearly the metal and its quality of surface — as, for example, in bassetaille, where the whole effect of the process is due to the transparency of the enamel. The translucent are those which are not transparent, but which admit the light through them; the opaque are those which do not.These enamels are composed of a simple flux, and also of a flux combined with oxides of metals. The flux is composed of silica — that is, of powdered flint or silver sand; minium, which is red lead; nitrate, or carbonate of soda, or potash, all melted together in a crucible until there are no bubbles left in it. This flux, which is the base of all enamels, is combined with different metallic oxides in various proportions. To a certain point, beyond which no combination occurs, the more oxide fused with the flux, the darker in tone and richer in colour will the enamel become, and vice versa. Transparent enamels are made opaque either by the addition of calx, which is a mixture of tin and lead calcined, or else by arsenious acid, that is to say, of white arsenic. The flux when combined with a precipitation of gold and tin, called purple of Cassius, gives a beautiful purplish red; when combined with oxide of copper, green, blue, and red may be obtained: with oxide of cobalt, a blue; with iron, a brown or orange; with manganese, a purple; with silver and gold, an orange red; and with stannic acid or oxide of tin, an opaque white.
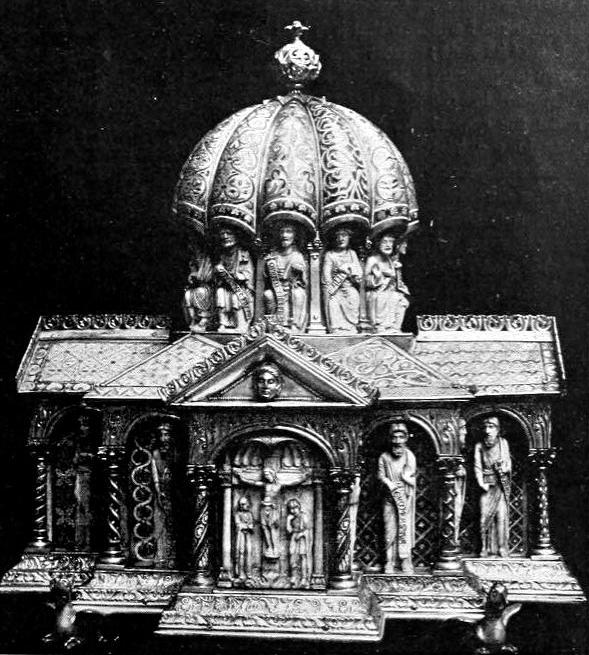
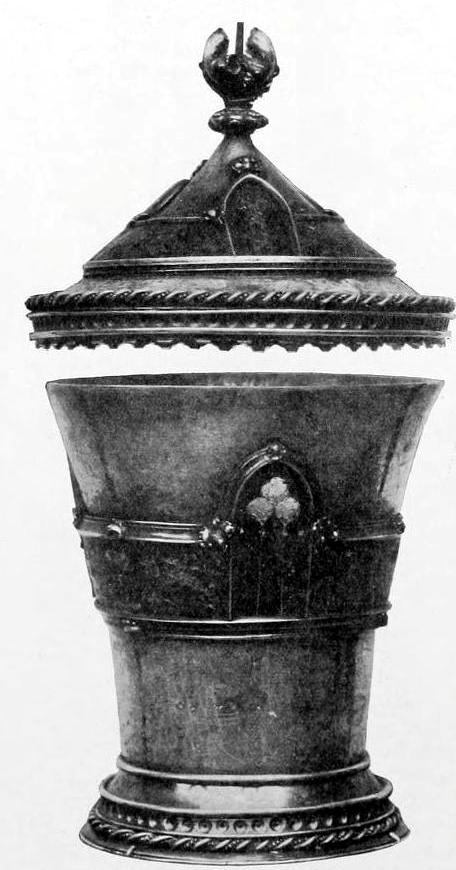
Left: Reliquary, illustrating the use of hamplevé enamel. Right: Silver gilt beaker with “plique à jour” enamel. (Burgundian, early fifteenth century).
These enamels can be mixed together in the crucible to obtain any variety of colour. All of them are made by the flux and the oxides fused together at an even temperature, and the quality of their tone is determined by the intensity of their fusion and the intimacy of their combination. There is no limit to the range of colour, except that vermilion and lemon yellow cannot be obtained.
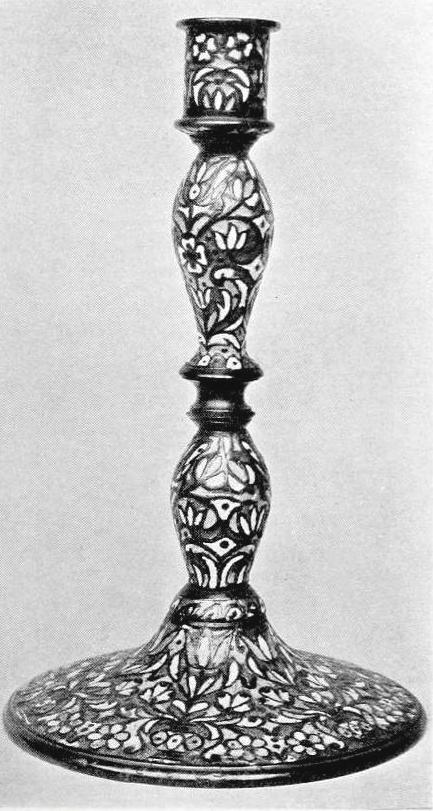
Candlestick of champlevé enamel on brass. (English seventeenth century).
Enamels are either "soft" or "hard " — that is, they are either easily fused at a comparatively low temperature or they require a great heat. An enamel is perfect when the combination of the component parts of the flux, together with the oxide of metal, is such that there is no difference of colour, opacity, or transparency, throughout the whole mass. The best way to determine whether the combination is perfect is by dipping a copper rod into the crucible and withdrawing it with a part of the enamel sticking to the end; pull out the rod some distance, so that a fine thread of enamel may be formed; then pass the thread between the thumb and finger, and the slightest difference of surface will be detected throughout its length. The quality of the colour will also be perceptible. Now, the harder the enamel the greater the quantity of silica contained in it, and the greater the resistance to atmospheric or chemical action; the softer the enamel the greater its percentage of lead and potash, and the more liable it is to be decomposed by atmospheric influences and chemical agencies. It is very tempting to use soft enamels, for at first they look so much more brilliant, and are so much easier to work with, but there are dangers to which the harder kinds are less subject. Thus, when in a state of fusion in the furnace, dust and foreign matters may injure them greatly, dulling the surface and destroying their transparency. The soft kinds of enamel contain a large quantity of lead, and sometimes of borax — a substance that renders them utterly worthless. The brilliancy and perfection of an enamel will depend upon the intimate combination of its parts; and this depends largely upon an even temperature being sustained throughout its fusion in the crucible. It is better not to make the enamel from the raw materials, but to obtain the best optical Crown glass, and add minium and potash in proportions which I shall give further on. It is advisable to use enamels made with the same base or flux, to prevent their cracking; for instance, an enamel heavily charged with lead, if fused upon one that is made with a large proportion of silica, will crack very readily, and probably peel off in course of time. It is impossible to obtain all coloured enamels with the same flux as their base, so that it is best to employ those fluxes which are most nearly allied. After some experience it is possible to ascertain by touch and weight and fracture the kind of substances composing a piece of enamel.
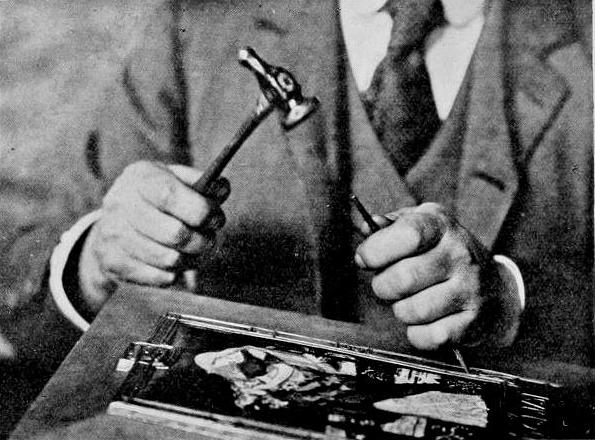
Chiselling cells in the border pf a frame for the insertion of enamel.
Silica is procured from flint or sand; if from flint, the white flints and the black are better than the yellow, as they contain less iron. The process of clarification is interesting. The flints are made red-hot, then thrown into cold water; after this they are pulverised, sieved, and washed several times. This done, they are treated with hydrochloric acid to remove all trace of iron, and finally washed once again in water to remove the acid. Silica has the property of increasing the hardness of an enamel. The minium or red lead is the orange-red coloured oxide of lead, which is easily procurable. It has the power to soften enamels and to give them a greater degree of expansibility. The compositions of flux are as follows: —
First, for copper flux and gold flux, take — 4 parts of silica, 6 minium, 12 nitrate of potash; or 4 parts optical glass, 3 minium, 6 nitrate of potash.
Second, for silver flux, take —
4 parts of silica, | 6 minium, | 20 nitrate of potash. |
Cobalt, oxide of cobalt | 1 to flux | 50 parts. |
Green, black oxide of copper | 1 to flux | 40 parts. |
Yellow, chloride of silver | 1 to flux | 12 parts. |
Ruby, purple of Cassius | 1 to flux | 112 parts. |
Ruby, chloride of gold | 1 to flux | 200 parts. |
Purple, peroxide of manganese | 1 to flux | 200 parts. |
purple of Cassius chloride of silver Orange red | 1 to flux | 20 parts. |
White, calx (calcined tin and lead) | 16 to flux | 20 parts. |
Opalescent yellow, from chloride of silver and arsenic | 6 to flux | 24 parts. |
Yellow, oxide of antimony | 6 to flux | 22 parts. |
Calx is prepared from tin and lead, not only by melting them together, but by exposing them whilst melting to the air, in order that the metals may oxidise. White can be modified to any extent by the addition of a more densely coloured enamel, to make it grey or brown, as the case may be. To do this the coloured enamel is pulverised to a granular state, then put in a crucible and melted in the furnace; to this is then added the pounded white enamel, the crucible being stirred all the time, and the mixture is ready for the furnace. It may require several firings and good * It is necessary to note here that every enamel requires a special treatment in the method of its manufacture, and that ii would require a large volume to discuss the making of enamels in all its subtleties. The receipts printed above give only a broad idea of the subject. stirrings before the ingredients become thoroughly combined. As soon as the combination is complete the mixture is poured into a tin of water.
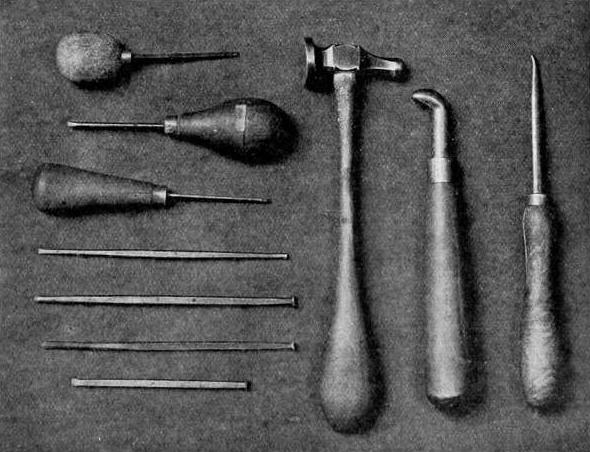
Steel tools — chisells, scoopers, graver, chaser's hammer, and burnishers..
The enamel substances being made, the next step is to prepare them for use upon the metal. This is done in the following manner. Take an agate mortar measuring 5 ins. in diameter, fill it half full with distilled water, and add a small quantity of enamel; then place the mortar over a leather pad, and holding an agate pestle firmly in the left hand perpendicularly over the enamel, strike the top of it with a wooden mallet, taking care to avoid the sides of the mortar. Continue this operation until the enamel is smashed into fragments. Then take the pestle in the right hand, and hold the mortar firmly with the left, still on the leather pad; rotate the agate end of the pestle on the enamel, and go on doing so until the enamel is pulverised to the finest powder. Meanwhile the water has become milky, so pour it away, and add a fresh supply, repeating this part of the work until the discoloration of the water disappears. Thoroughness of washing is of the utmost importance in the preparation of a clear transparent enamel. Opaque enamels do not require so much washing.
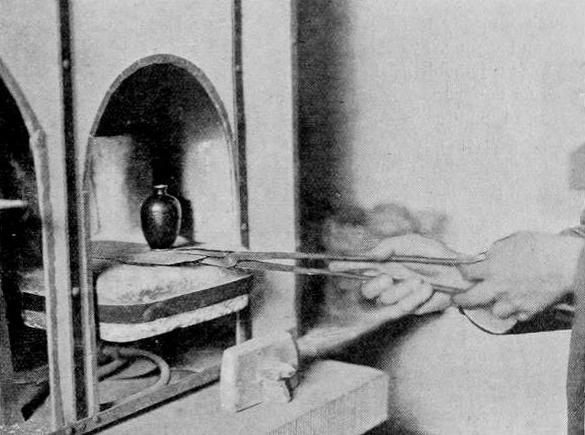
Placing an enamel vase into the furnace.
And now, leaving the enamel corked up securely in a clean bottle, to prevent any dust or foreign matter from getting in, let us see how the metal is prepared. The first process which I shall describe is that known as champleve'; the next bassetaille; then cloisonne; then painted or Limoges enamels; and, last of all, miniature painting in enamel. Champleve enamelling is so called from the two words champ, a field, and leve, raised. The field or ground of melal is cut away, leaving bands of metal to form the outlines of the design; then with enamel the part cut away has to be raised flush to the surface of the outlining bands, so that the whole is a uniform surface. The first requirement is a pitch block, that is, a piece of wood on which a composition of two parts of pitch, six of plaster, and one of tallow, all mixed together in a saucepan over the fire, is poured to the thickness of an inch. In the case of large work the wood must be strong and heavy, but when the work is minute the pitch or cement must be placed upon the end of a stick.
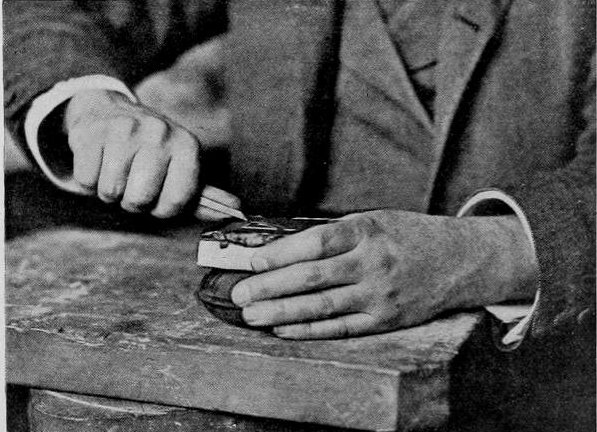
Usual method of cutting cells with a scooper. Observe the position of the hands. The left hand moves the piece on the sandbag horizontally against the fixed point of the tool, which is held rigidly.
There are two ways of using the tools, concerning which it is now necessary to speak. For large work a chaser's hammer and long steel chisels must be employed; for small work the graver or the scooper is held rigidly in the right hand, and by a firm, restrained pressure the metal is gouged out, as shown in the illustrations. It is very necessary to keep the tools sharp and clean. The design is either drawn on the metal with a hard black lead point or else transferred upon it by means of transfer paper in the usual way, and then the lines are traced with a fine graver, giving a faint hair line of the utmost exactitude. This done, the line is cut deeper with a V-shaped tool, about one-thirtysecond of an inch to one-sixteenth, the depth being governed by the strength of colour required. In transparent enamelling on silver or gold, for instance, the darker the colour used the deeper the cutting ought to be — within limits, of course — one-sixteenth being quite deep enough for an objectof any size. When this depth is exceeded the enamel is so thick that it flies off. A trench having thus been chiselled all around the spaces, leaving the line of design untouched, the spaces themselves have to be cut to an equal surface, at the same depth as the surrounding trench — that is, one-thirty-second or one-sixteenth of an inch below their present surface. The metal ought to be fairly thick, either No. 14 or 16 metal gauge, and for larger pieces No. 18 or 20 metal gauge.
This surface, which has been chiselled or " scorped," must now be cut into a roughened surface, so as to give it a strong key for the enamel to hold on by. Many varieties of textures and patterns may be given to this keying of the surface, which in the case of transparent enamels is of very great importance.
As soon as the surface is well keyed, the metal plate is taken off the pitch by means of a very gentle heat from a blow-pipe flame. The back is cleaned thoroughly with paraffin, and then treated with a hot solution of crystal soda, after which it is finally cleaned with methylated spirits. Then, upon the parts which are cut out, the chosen enamels, mixed with distilled water, are laid with a small spatula. If the piece of work is large, and may take several days or weeks to fill in, it is better to add a few drops of a weak solution of gum tragacanth or of quince-pips, so that those parts which are set and dry may not be disturbed by the subsequent fillingin of other parts. This being finished, it is necessary to fire — that is, to fuse the enamel. For this purpose I find that a gas furnace is greatly superior to any other kind. It is cleaner, it requires less attention, and it gives a more uniform heat, and in many ways saves a good deal of time. If, however, gas cannot be obtained, a furnace heated by coke or by petroleum is sufficiently serviceable. Besides a furnace it is necessary to have supports or "planches" for holding the enamelled metal plate. These may be made of iron, coated with chalk, loam, silica, or rouge; or they may be of fireclay, coated with the same substances. It is better to heat the "planche ' before placing theenamelled plate upon it ready for the furnace. The tongs should be long and firm, with long, thin, pointed fingers.
When the muffle of the furnace has reached a pale orange red, the second part of the process begins. It consists in taking firm hold of the planche, with the enamelled plate upon it, and very gently placing it into the furnace. Then observe it carefully, on no account leaving the furnace at all until the enamel is fused; and when the enamel shines equally all over, withdraw the planche carefully, and lay it gently on the top of the furnace or upon some other warm place near at hand. You will now see that the surface of your enamel is very irregular, so you fill up all the hollow parts, and fire again. This process is to be repeated until the plate is as regular in surface as you can get it. If there are still some irregularities, you take the plate and, while holding it firmly in the left hand under a tap of water, you file it with a corundum file, repeatedly washing the plate and scrubbing it clean with a hard nail-brush. This will give you an even, unpolished surface. To regain a bright surface it is necessary either to put the plate into the furnace again and fire it as before, or else to polish it. This entails a constant rubbing — first, with a smooth corundum and water until all the roughest scratches are out of the enamel; next, with pumice-stone and water until the surface is much smoother; then with water-of-ayr stone and water, when a dull, smooth surface will appear; then crocus powder and water, with a stick , and leather; and, finally, with rouge, either on a buff fixed on a lathe, or by hand with rouge and chamois leather. This is a laborious process, but it produces a result that no fire polish can give, and is one of the chief charms of the old champleve work. The metals which lend themselves readily to this class of work are gold, silver, and copper. Copper is the one which has been most commonly used at all times. The best copper for this purpose is not pure; it is composed of i lb. of pure copper to i oz. of zinc. The alloy of zinc prevents the edges of the copper from oxidising into a rough burr, which is most unpleasant to work with. ( To be continued. )
Bibliography
Fisher, Alexander. “"The True Art of Enamelling on Metals” The Studio Part II: 23 (1901): 88-96. University of Toronto copy made available online by the Internet Archive. Web. 25 January 2012.
Last modified 25 January 2012