In transcribing the following passage from the online version I have expanded abbreviations and added paragraphing, subtitles, links, and illustrations. The illuminated initial letter with which the article begins comes from the original, though I have added red to it. — George P. Landow
The Steel Pen Trade
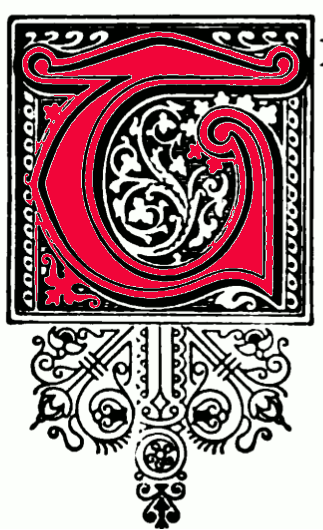
HE second quarter of the nineteenth century witnessed the introduction of several entirely new branches of local manufacture. The first of these was the steel pen trade, which, in its modern form, came into being between 1825 and 1830. There had been metallic pens before that date, but from the tedious method of their manufacture, and the hard, unyielding nature of the pens produced, this branch of industry gave little promise of becoming one of the staple trades of the town. The history of the introduction of a more rapid and satisfactory method of production, and of a practicable steel pen, is shrouded in some degree of mystery, and the invention has been claimed by, or on behalf of, several persons. Several patents were taken out between 1820 and 1830, by Mr. James Perry, of Red Lion Square, London, for improvements in the manufacture of steel pens; and during the same period, four Birmingham men were simultaneously engaged in experiments in the same direction. These were, the brothers John and William Mitchell, Josiah Mason, and Joseph Gillott. The brothers Mitchell seem to have first succeeded, by a tedious method, in producing pens of a satisfactory character, although Josiah Mason and Joseph Gillott, both unknown to each other, did much to help forward the new industry into the domain of practical manufactures by the use of the press and the die (which were, up to that time, used chiefly, if not solely, in the button trade) in the manufacture of pens.
That the process of manufacture was as yet far from complete, is evident from a letter written by Mr. Alderman Manton, in 1866, wrhich Mr. J. T. Bunce quotes in his Memoir of Sir Josiah Mason. The writer says: “In a badly constructed and most unsanitary manufactory at the back of Suffolk Street, I witnessed (1823) the process of making silver and steel pens. As both metals were manipulated in the same manner, one description will serve. It will be remembered by a few that at that time there was a pattern of silver pencil-case somewhat extensively manufactured, in which, in addition to the pencil, a pen-knife, pen, and tooth-pick were provided. The pen-knife was supplied by two brothers, Joseph and William Gillott, who at that time rented a small shop in the corner of the yard belonging to the rolling mill of George and P. H. Muntz, in Water Street, and from whose engine they obtained the small amount of steam-power needed.
“The process of making the pens was as follows: Two narrow strips were cut from the sheet of silver or steel; they were then, by the help of the hammer, and a lead cake, or piece of hard wood, curved; and afterwards the two strips were placed opposite to each other, on a well-polished steel wire, and drawn through a draw-plate (the wire and plate being supplied by William Billinge, a celebrated tool manufacturer, occupying premises near the top of Snow Hill). By the aid of a press a small hole was made, at a distance of half an inch, or five-eighths, from the end; the slit was then made by a fine saw made of w’atch spring. A bent pair of shears was used for cutting the end of the strips into the shape of a pen, and a half round or a smooth file was used for finishing the pen. The pen was then sawn off the strip by the same saw which was used for slitting the pen. The only hardening process was the friction of the draw-plate and the steel wire. I not only witnessed the process, but was a manipulator. The cost of making at that time by a journeyman was about twopence each; by an apprentice, about one-third of that amount. Within less than thirty years of that time, in a manufactory adjoining my own, pens were made and sold at twopence per gross, and a box containing them into the bargain!”*
For a long time the steel pen had to encounter the prejudice which the earlier hard metallic pens had engendered in the public mind, and it was largely due to the indomitable perseverance of Mr. James Perry that it was forced into general use. After some years of experiments he had been brought into connection with Josiah Mason,* who thereafter supplied him with all the pens bearing Perry’s name. Mr. (afterwards Sir Josiah) Mason gives the following account of his introduction to Mr. Perry. “About 1829,” he says, “I saw in a book-shop window in Bull Street, Birmingham (Mr. Peart’s), nine ‘slip’ pens on a card, marked three and sixpence. The novelty, and the thought of Mr. Harrison’s pen, induced me to go in. Mr. Peart was writing with one of the pens. He said it was ‘a regular pin.’ I instantly saw that I could improve upon it, and offered to buy one of the pens. Mr. Peart, however, would not sell less than the whole card ; but at last he consented to sell me the one he was writing with, and so I bought the ‘pin’ for sixpence. I returned home, and made three pens that evening, and enclosed the best of the three in a letter, for which I paid ninepence postage—what a change now, to only one penny! I had not the slightest knowledge of the maker; but having, with difficulty, made out the letters stamped upon the pen I had purchased, to be ‘Perry, Red Lion Square, London,’ I sent my letter there. This brought Mr. James Perry to 36, Lancaster Street, the following day but one, by eight o’clock in the morning; and from that moment I became a steel pen-maker. Perry and Co. were my only customers for many years. From our first interview to the present time I have been the sole and only maker of the Persian and the steel B pens sold under Perry’s name.”t
Joseph Gillott is stated by one writer to have been led to take up the manufacture of steel pens from the fact of his having married a sister of the Mitchells, who had assisted her brothers in their work. “ She spoke to her intended husband of the nature of her occupation, and Gillott at once conceived that the press, the useful implement then used principally in the button trade, might, if proper tools could be made to suit, produce pens in large numbers very rapidly. With his own hands, in a garret of his house, he secretly worked until he had succeeded in making pens of a far better quality than had yet been seen. His process was one in which, unassisted, he could produce as many pens as twenty pairs of hands, working under the old system, could turn out. There was an enormous demand for his goods, and as he wanted help, and secrecy seemed needful, the young people married, and Mr. Gillott used to tell how, on the very morning of his marriage, he, before going to the church, made with his own hands a gross of pens, and sold them at is. each, realising thereby a sum of £7 4s” [Eliezer Edwards: Personal Recollections of Birmingham and Birmingham Men, p. 92.]
As a result of these early efforts on the part of the several persons mentioned, four large pen manufactories were established in Birmingham, namely that of Josiah Mason (whose pens for many years bore only the name of Perry), that of Joseph Gillott—who after removing from his original premises in Bread Street into Church Street, ultimately built the extensive manufactory in Graham Street—and those of John and William Mitchell. “When the British Association first met in Birmingham (in 1839),” says Mr. Timmins, “steel pens were almost unknown; but when the second visit was made, in 1849, the steel pen trade had risen to a very important place among the manufactures of our town. Between the two periods named there had been eighteen makers of steel pens, but these had been reduced to twelve in 1849...Although it is difficult to collect any trustworthy statistics of the extent of the steel pen trade in 1849, the following details may be relied on as an approximate estimate of the condition of the trade sixteen years ago [i.e. in 1850]—some twenty years after it had been introduced into our town. The number of factories then in operation was twelve; the men and boys employed, 300, the women and girls, 1,550; the amount of horse-power, 228, including 70 as representing out-work rolling; the number of pens made weekly, 65,000 gross; the steel used, 6½ tons per week ; the value of the slip or ordinary pens, from 6d. to 2S. per gross, and of barrel pens, from 8d. to 12S. per gross. Some few steel pens were then made in Sheffield and London, but since that time Birmingham has become the great scat of this manufacture, with some few exceptions” [Birmingham and the Midland Hardware District, 1866: art., The Birmingham Steel Pen Trade, by Sam: Timmins, pp. 634-5.]
Electroplating
Another important local industry which came into existence during this period was that of electro-plating. Up to 1840 silver-plating was effected by the fusion of a thin surface of silver with a base of copper, the combined metal being rolled out to the requisite size, thereby producing sheets of metal of a copper body with a silver surface, capable of being wrought up into various articles of a useful or ornamental character. This process involved the application of a heavy coating of the more precious metal, and the articles thus produced were of a handsome and durable character; such indeed was the richness of the plating that Matthew Boulton was in the habit of sending a small file with goods of this character manufactured at Soho, in order that his customers might test the quality of the metal.
Early in the present century, however, when the various uses of electricity were beginning to be dimly understood, the possibility of depositing one metal on another by means of the newly-discovered force engaged the attention of several scientific men,--among them Professor Jacobi, of St. Petersburg, Mr. T. Spencer, of Liverpool, and Mr. C. J. Jordan. There was at that time, too, a firm of gilt toy makers in Birmingham who were shrewd enough to perceive that these experiments in the laboratory might be put to practical use in the manufactory, and in 1836 and 1837 Messrs. George and Henry Elkington took out patents for ‘mercurial gilding,’ and in 1838 Mr. G. R. Elkington, in conjunction with Mr. O. W. Barratt, took out a patent for coating articles of copper and brass by a method involving the application of a separate current of electricity.
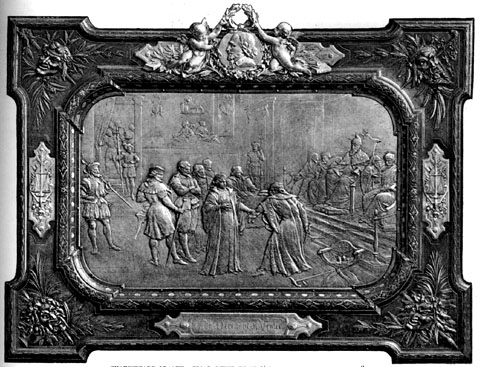
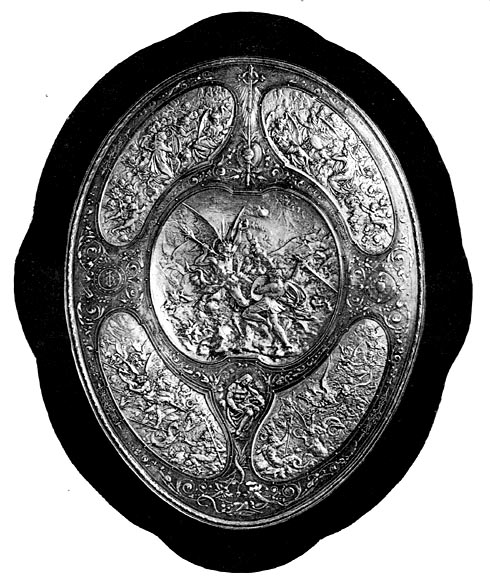
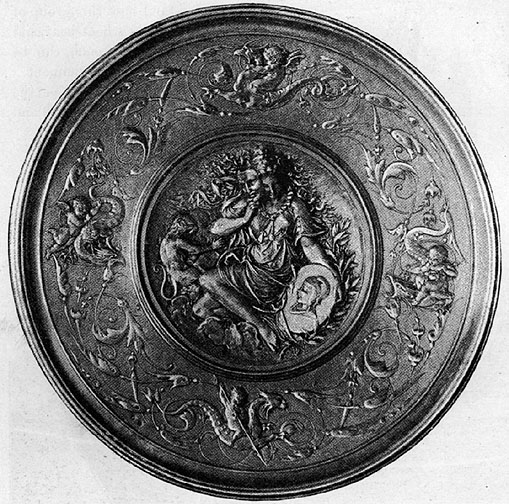
Three works manufactured by Elkington: Left: The Shakespeare Plaque — Trial Scene from the "Merchant of Venice". c. 1898. Middle: The Pilgrim's Shield. 1878. c. 1898. Right: The Tazza — Comedy. c. 890. All designed by Morel-Ladeuil (b. 1822).
In 1840 Mr. John Wright, a Birmingham surgeon, being engaged in some experiments in the same direction (in conjunction with Mr. Alexander Parkes, an experimentalist in the employ of Messrs. Elkington,) met with a passage in Scheele’s Chemical Essays which led him to hit upon a solution which has since proved to be the best of all liquids for electroplating—viz., the cyanides of gold and silver dissolved in cyanide of potassium- and having submitted this to Messrs. Elkington it was embodied by them in a patent for which they were at that time making application. By this discovery electroplating was brought into the region of practical industry, no longer a scientific recreation for the laboratory, but a new branch of manufacture which was destined to take its place among the chief industries of the town. This was not accomplished, however, without a severe struggle. The whole of the silver-plate trade, both in Birmingham, Sheffield, and London, set their faces against the innovation, and did their utmost to crush the new industry which they believed would ruin them if it proved successful.
The difficulties to be overcome were immense; not the prejudice of the trade only, but the metal which had to be worked wras stubborn, and very little known to the workman. Instead of ductile copper, which he had learned to fashion with the greatest success, he had to contend with a composite metal which, when mixed in due proportions, produced a metal beautiful in colour but very difficult to manipulate. From the first introduction of electroplating, the metal chosen on account of its near approach in colour to silver, was that which had been extensively used in the manufacture of spoons, forks, etc., and known under various names, as (German silver, nickel silver, albata, and many others, for each manufacturer tried to invent some new name for that which was really the same thing. [“Birmingham and the Midland Hardware District.” The Plated Wares and Electro-Plate Trade, by W. Hyland, pp. 488-89]
But the new method of production had its advantages. The old silver-plated articles had to be made up from the silver-coated sheet of copper, and consequently the ornaments, handles, and other projecting parts had to be put on to the already plated body of the articles, whereas the electro-plate wares were completed and polished before receiving their coating of silver, and might therefore be made up and laid aside in the manufacturers’ warehouse until they were ordered, and undergo the process of plating at the last moment before being despatched to the customer.
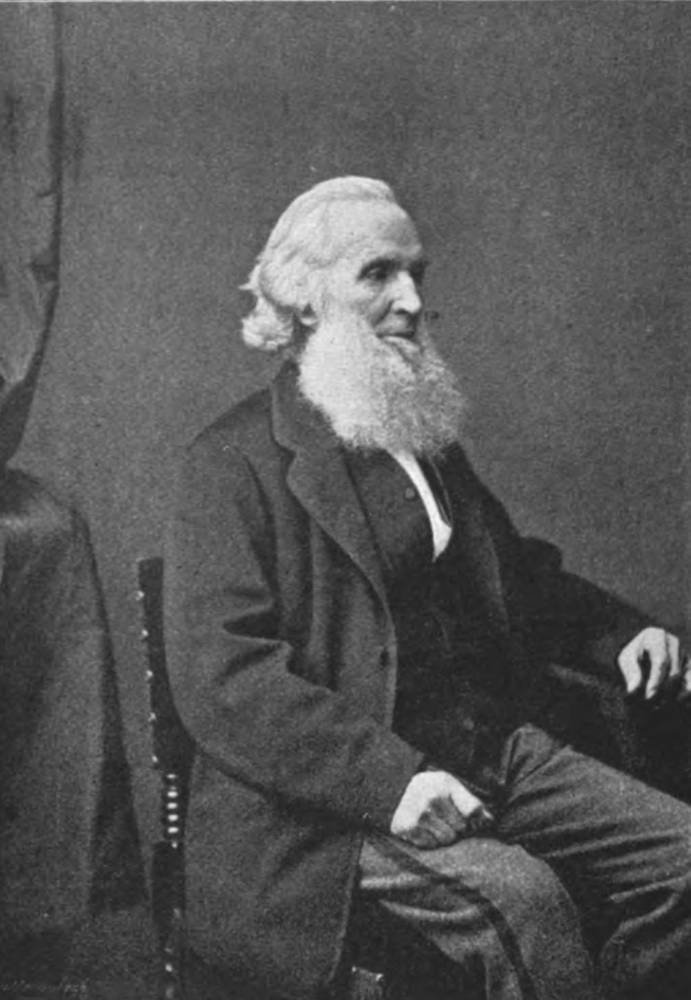
Sir Josiah Mason from a photograph by Draycott.
The Messrs. Elkington were joined in 1842 by Josiah Mason, whose business capacity, energy and enterprise were of great service in bringing the new industry to the front. “What Boulton had been to Watt, in an earlier period of the history of Birmingham manufacturers,” says Mr. Bunce, “Mason, in a certain sense became to Elkington. . . . His efforts were consequently directed to the work of making the new trade pay. Being embarked in it, he undertook this with characteristic energy, and with a power of concentrated labour which few men could have equalled” [Memoir of Sir Josiah Mason, p. 129]. The new partner designed the new premises for the manufactory, in Newhall Street, to which distinguished visitors from all parts of the world have been attracted. For the part which Mr. Wright had taken in bringing the process of electro-plating to a successful issue, that gentleman received a royalty of one shilling for every ounce of silver deposited; but on his decease, which took place soon afterwards, an annuity was paid to his widow.
Another important discovery in the same direction was made by Mr. Woolrych, of Birmingham, who in 1842 patented the first dynamo for use in plating instead of the galvanic battery. This process was taken up by Mr. Thomas Prime, of Northwood Street, and here, introduced by Dr. Percy, the celebrated metallurgist, Michael Faraday saw for the first time his discovery of the magneto-electric current applied to the electro-deposition of silver. The first dynamo used for this purpose has within recent years been presented by the son of the manufacturer to the Corporation of Birmingham, and is now preserved in the Aston Hall Museum.
The electro-plate trade speedily obtained a prominent position among local industries. The process of electro-depositing was applied to other purposes beside that of coating articles of German silver or brass with a more precious metal; by its aid reproductions were obtained of fine examples of art metal work by the great masters, Ghiberti, Cellini, Caradosso, and others. Gradually the Elkingtons gathered around them a school of art workmen little inferior, if inferior at all, to those of the middle ages or the Renaissance. Their show rooms in Newhall Street became a veritable museum of the fine arts, and their reproductions have been among the chief features of interest in all the great international exhibitions which have been held during the past thirty years or more. The two branches of this trade found employment, and largely added to the demand for skilful workmen, and originated a superior class of artizans. From the census of 1841 it appeared that there were 10,755 ‘goldsmiths, jewellers, and silversmiths’ (including platers) in Birmingham; but through the development of the electro-plate trade that number was greatly increased during the following decade, and at the census of 1851 it was found that these branches of local manufactures employed 13,250 persons.
John Hardman and Manufacturing Stained Glass
The Gothic revival, which had its beginning about the same time as the high church movement, and partly as a result of that movement, exercised a considerable influence on local manufactures, more particularly as regards art metal work and the production of stained glass. In 1837, John Hardman, of Paradise Street, became acquainted with Augustus Welby Pugin, who had done so much to bring about the Gothic revival, and the friendship which sprung up between the two men resulted in Mr. Hardman’s undertaking to start metal and glass works on mediaeval principles. This new trade, coming into existence at the opportune time, rapidly developed into an important branch of local industry, and “ exercised an influence on metal-working generally closely akin to that of the Pre-Raphaelite movement on painting. It has had the effect of making metal-workers think, apparently for the first time for some centuries, and has been the means of creating a superior class of skilled artificers, who claim for themselves a special department of metallic industry. Wherever metal work on mediaeval principles is now practised, its origin can be traced to Birmingham as the parent stem, and a large portion of the artisans first employed in it by other firms and manufacturers have acquired their skill and learnt the secrets of their art at the works of John Hardman” [Birmingham and the Midland Hardware District; “The Revived Art of Metal-Working,” by W. C. Aitken, p. 538].
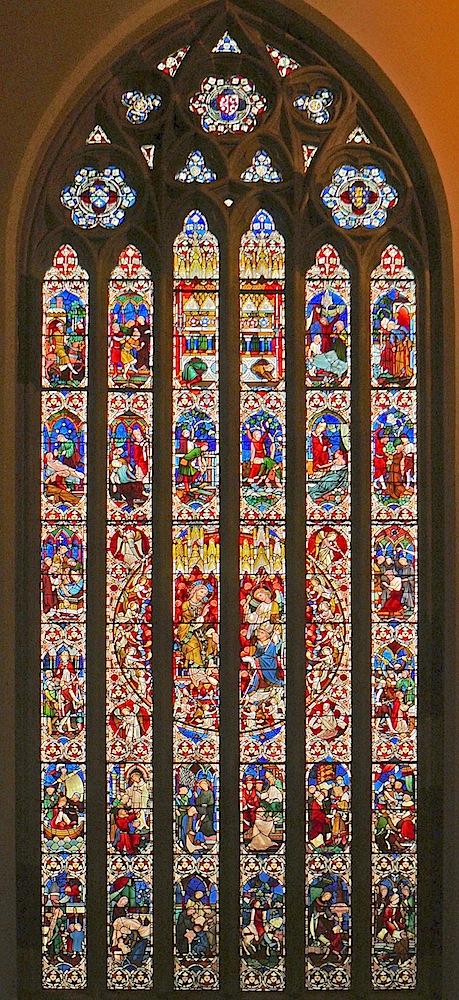
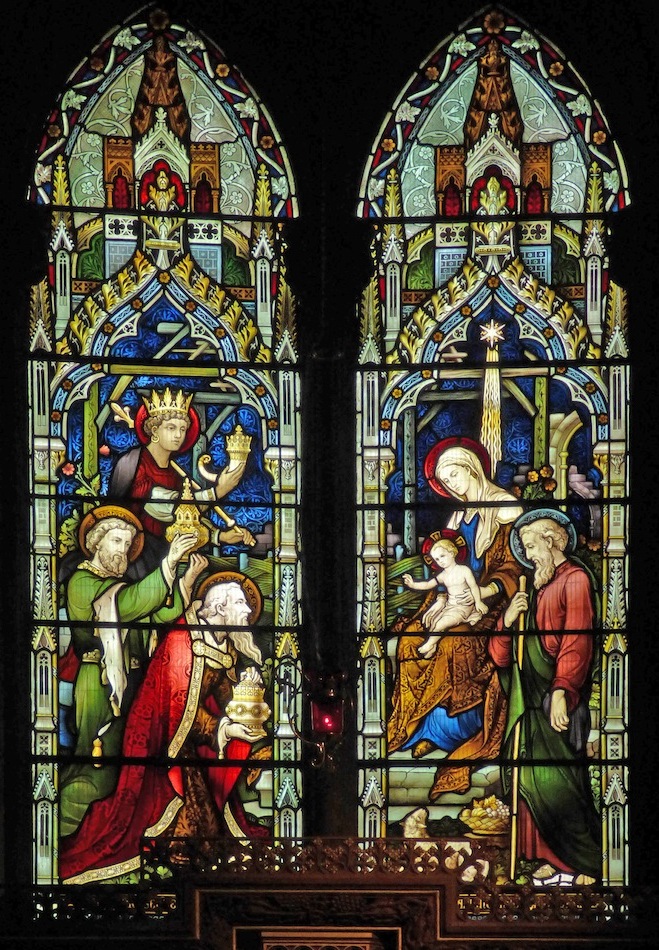
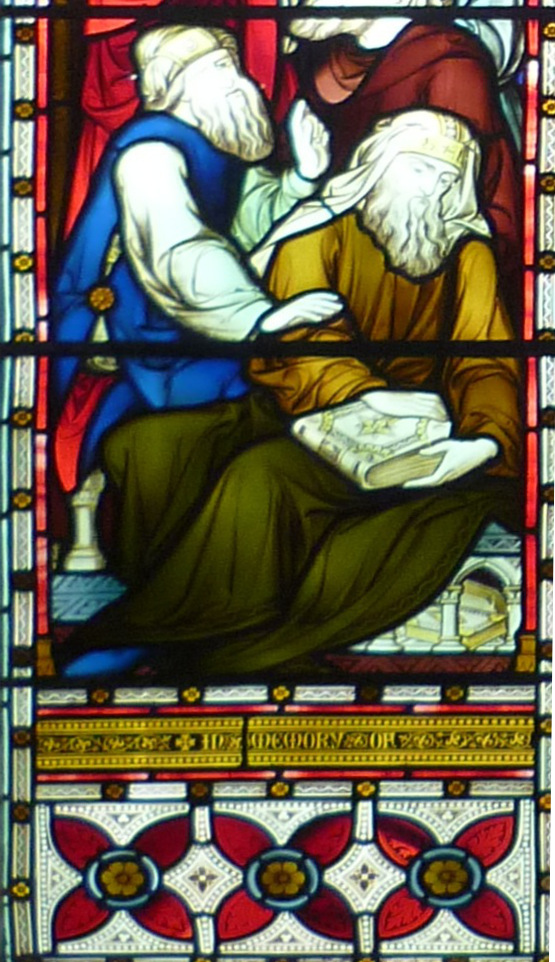
Three windows by by John Hardman & Co. Left: The Flanagan Window at St Chad's R.C. Cathedral, Birmingham. Middle: The Coming of the Magi. 1864-69. Apse, Holy Trinity, LLandudno, North Wales. Right: Raising Jairus's Daughter, installed in 1874 in William Butterfield's St Matthew's Church, Ashford, Surrey. [Click on images to enlarge them.]
In the stained-glass department of the new manufactory Mr. Hardman had the assistance of several qualified craftsmen, among them two sons of Robert Henderson (a Birmingham glass-painter of the Eginton School), Mr. Hinckley, and others. In course of time a school of artists in stained glass was formed at the works of Mr. Hardman, gathered mainly from among the young artisans of Birmingham.
Other works for the production of stained-glass existed in Birmingham during this period. Messrs. F. and C. Pemberton still preserved the traditions of Francis Eginton, and executed a good deal of good work, of the smooth glass order, chiefly for mansions and secular buildings. Messrs. Chance Brothers and Co. also carried on this branch of glass manufacture, under the direction of M. Bon temps.
We have devoted this chapter largely to the consideration of three or four special developments of local manufactures during the second quarter of the nineteenth century, and it will not be necessary for us to deal minutely with the older trades which were still carried on during this period. As Mr. Jaffray observes,
the great majority of the population were employed as they had been a century before. There were almost the same staple trades, although some had died out and were nearly forgotten, except by very old men or in the traditions of workshops; and some new branches of industry had sprung into existence, excelling the old in the magnitude of their operations, and rivalling them in the multitudes of people they employed. Still the mass were engaged as they had heretofore been, although upon a larger scale.[Hints for a History of Birmingham, chap. xlix]
Related material
- Victorian Technology (homepage)
- Decorative Arts and Design in the Age of Victoria (homepage)
- Joseph Gillott's pen-nibs, sheet steel, and the writing revolution
Bibliography
Dent, Robert K. The Making of Birmingham: Being a History of the Rise & Growth of the Midland Metropolis. Birmingham: J. L. Allday, 1894. Birmingham: Hall and English, 1886. 398-403. HathiTrust online version of a copy in the University of California Library. Web. 4 October 2022.
Last modified 12 October 2022